Multi-Tasking CNC Machine Centers
Snyder Industries’ multi-tasking centers include two (2) Mazak Integrex E-1060’s, six (6) Toshiba TUE-150S’s, two (2) Hyundai-Kia SKT300M’s, one (1) OM NeoAlpha 10, and two (2) Samsung SL-6500AM5/1000 machines. Some of Snyder’s multi-tasking centers are featured below.
Mazak Integrex E-1060
The Mazak 5-axis system has rotary tables and tilting spindles capable of turning, milling, boring and drilling large diameter work pieces with a single setup, offering a true “done-in-one” machining process. Each E-1060 machine features a robot and shares a 24-station, two-level pallet system with enhanced loading and unloading capabilities.
The Paletech pallet-loading system serves the machining center with parts that have been pre-loaded, programmed, queued and prioritized. The Mazak system automatically unloads the finished part and loads the new part in seconds.
Each Mazak has a 120 Cat-50 capacity tool carousel and automatic tool changers preloaded for different jobs or to provide backup tools as needed.
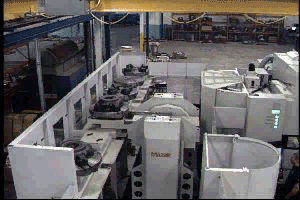
The entire operation is overseen at the E-Tower command station which gives the operator complete control and constant reports on the machining progress. The system can also be accessed and monitored off-site if necessary.
In addition, these Mazak units are equipped with support systems that enable hours of continuous uninterrupted operation.
Toshiba TUE-150S
Snyder Industries has two (2) additional TUE-150 machines to increase capacity. Currently, six (6) machines are used to turn and mill components for our largest customers.
These machines are capable of adding features to parts as large as 79” in diameter, 61” in length, and weighing as much as 17,600 lbs.
S-Type has a live spindle that performs drilling, tapping, and boring operations.
CNC Milling Centers
CNC Milling Centers
Snyder Industries’ milling department consists of several OKK and Mazak milling machines. With designated fixtures, they are able to run parts vertically and horizontally. Each of our mills have Fanuc CNC controls.
OKK Mills
OKK Milling centers at Snyder can hold parts as large as 77” OD, 59” OAL, and 11,000 lbs. Each of our seven (7) horizontal mills are equipped with a pallet system and operated with Fanuc CNC controls. Snyder has machine helpers that can assist with set ups on these pallet machines.
Five (5) vertical and seven (7) horizontal OKK mills are able to run complex features. The operator can hold finished dimensions to tolerances of .0002” on size and location.
Mazak Mills
Snyder’s Mazak mills are equipped with Paletech loading systems, which allows the operator to focus on keeping the machine running throughout the day. The two H-800X machines are fed by a 16-pallet loading track.
The Mazak Ultra-650 has designated tombstones and other fixtures that are used to reduce setup times on its loading system.
Each Mazak mill has their own 120 or 160 capacity tool carousel and automatic tool changers pre-loaded for different jobs or to provide backup tools as needed.
Gun Drill
Snyder Industries has the ability to deep hole drill up to 60” depth using a Tarus gun drill milling machine.
Snyder Industries’ milling department can satisfy most of your machining needs, from large amounts of stock removal to holding a tight tolerance bore location.
CNC Turning Centers
CNC Turning Lathes
Snyder Industries’ turning department operates both vertical and horizontal lathes in addition to their multi-tasking machine centers. Fanuc CNC controls are used on the 24 machines manufactured by Doosan, Samsung, Ikegai, Hancook, OM, and Hyundai-Kia. These machines offer diameter capabilities from 2” to 59” and length capabilities of up to 57” with the ability to machine to tolerances of 0.0002”.
Samsung SL-6500AM5/1000
Some of Snyder’s most recent equipment additions have included two (2) Samsung SL-6500AM5/1000 lathes that allows them to run detailed jobs complete within their cell. This new investment has helped limit material handling and improved quality and delivery. These machines are able to machine parts as large as 35” in diameter and 39” in length.
Other lathe cells in the plant allow operators to set up and run large quantity orders. This is especially cost effective for customers that have designated KanBan parts.
Using hydraulic and manual independent chucks, we have multiple fixture set ups to run any type of product.
Snyder Industries’ turning department can satisfy all of your machining needs, from large amounts of stock removal to holding a tight tolerance diameter.
Also see our Multi-Tasking CNC Machining Centers for more turning services.
Gear Cutting, Shaping & Hobbing
Gear Cutting, Shaping, & Hobbing
Snyder Gear changed its name to Snyder Industries in 1990. Since this time, they have not stopped adding and improving the gear capabilities. As technology improved, capital investments has kept Snyder ahead in the gearing market. Through the years many investments have been made in CNC gear shaping and hobbing to improve quality and production times for large ring gears.
Shapers
Of the nine(9) CNC Gear shapers in the Snyder facility there are one (1) Gleason P500s, five (5) Gleason P600/800S, and two (2) Gleason P800/1200S machines in line.
The largest machines are capable of cutting external gears as large as 51” OD with a 15” stroke.
Four (4) manual Fellows shapers are still in the plant that can be used when needed.
Hobs
Two (2) CNC Gleason Gear Hobs and three (3) Barber Coleman horizontal Hob machines help with additional gear capacity for rings gears and splined shafts.
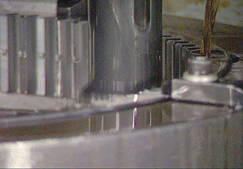
Tool Sharpening
Snyder has invested in two (2) cutting tool grinder machines to help with sharpening tools for the gear shop and also throughout the plant. The Star PTG1 and Schneeberger Aries NGP are in a cell to assist any sharpening needs for the floor. This has been extremely helpful with turn-around time and keeping key machines operational.
Snyder’s CMM’s are capable of running gear charts on machined gear to ensure specifications are met. See CMM Inspection for more information.
After gear cutting, parts can be moved to their in-house heat treating facility to induction harden the machined teeth. See Heat Treating for more information.
Metal Heat Treating
Metal Heat Treating & Hardening
Snyder has its own in-house metal heat treating and hardening division which allows for further control over quality and production.
Heat Treating
Computer controlled atmospheric heat treatment is another beneficial aspect of Snyder Industries / Great Lakes Metal Treating.
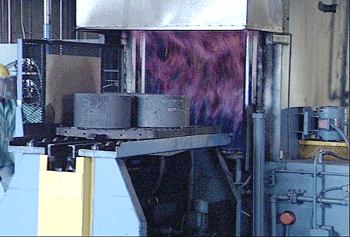
Two Surface Combustion AllCASE Batch Integral Quench Furnaces, each with a capacity up to 4,000 lbs, perform treatment processes such as normalizing, stress relief, oil quenching, annealing, carbon restoration and gas carburizing.
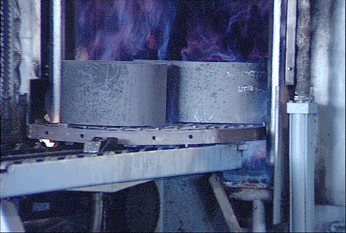
The furnaces operate under an endothermic atmosphere which yields treated parts with extremely clean surface finishes to ease the subsequent final machining processes. Presently processes have been developed for treating numerous alloys in various shapes and sizes. ‘Stop-off’ paint can be applied to protect from unwanted treatment on particular surfaces.
Induction Hardening
As a branch of Snyder Industries Inc., Great Lakes Metal Treating was created to utilize today’s new technologies. The Induction department hardening is no exception.
Within this department there are four NATCO induction hardening machines; three horizontal and one vertical. There is also one Inductron II TOCCO induction hardener.
NATCO uses the Delapina method by submerging the gear teeth under the quench to allow an instant quench for maximum hardness and minimal distortion. NATCO has the range to perform from a 2 pitch to a 6 pitch gear, due to the ability to vary frequency from 150 KHz to 300 KHz with a power of 25 KW.
All of Snyder’s vertical Natco machines are equipped with Allen Bradley PLC Compact controls which enables for precise and consistent case depths.
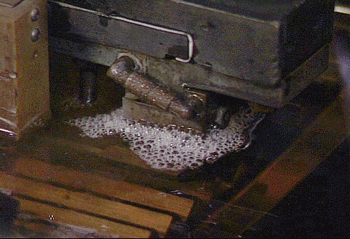
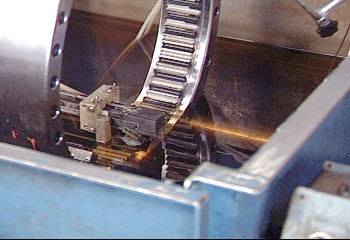
Effective case depths of up to .250″ with a hardness of 60 HRC can be achieved. TOCCO uses a 10 KHz frequency with an output current of 200 KW. This process can reach up to .375″ in case depth with a hardness of 58 HRC.
Each machine is programmed to specifically meet the customer’s request. Before an order is processed, a sample is run, then cut and analyzed to assure the required specifications are met.
We can harden gear teeth precisely to the depth required. We are the complete machine shop, this allows us to design and construct the fixtures and inductors to harden our customers’ parts. All metallurgical analysis is performed in-house by our trained technicians.
Shot Peening
Also included at the Snyder Industries / Great Lakes facility is a computerized Empire Abrasives shot peening system, where steel shot is used to meet the design requirements of the customer under accurately controlled settings.
Hardened gear teeth and specified areas of the machine part are peened to increase fatigue strength and life of the gear. An Almen strip test is used to verify the intensity for each job order. Our shot peening process is certified to the Mil standard 13165-C.
CMM Inspection
Snyder Industries maintains its reputation of excellence by its strict quality control requirements. High tech measuring devices and experienced personnel insure that the highest standards are met.
Snyder Industries runs three Coordinate Measuring Machines (CMM) in a 1,864 sq ft climate controlled area to ensure accurate measuring. Each machine digitally records the information of each measurement.
The CMM probe is capable of making many measurements quickly and efficiently. This robotic feature enables Snyder Industries to provide its customers with the most thorough records available.
Through the use of the Coordinate Measuring Machines, Snyder Industries can check the tolerances of its manufacturing down to .0002″ and give its customers a printed report showing that the parts do meet or exceed their requirements.

Snyder Industries is registered to ISO 9001:2015 by Steel Related Industries Quality System Registrar, Inc.
Current Registration Period: July 15, 2021 through July 14, 2024
Download Snyder Industries ISO Certification (PDF 137k)
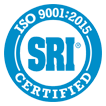
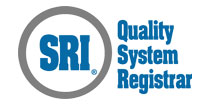
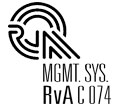
Snyder Industries Quality Control Policy
We are committed to developing, manufacturing and delivering on-time, world class products and services, which consistently meet or exceed our customers’ requirements. In partnership with our employees, customers and suppliers, we are dedicated to continuous improvement in manufacturing, quality and customer service.